Facility Features
All warehouse storage areas are network-monitored and automatically conditioned to keep relative humidity below 50% to prevent exposure and potential moisture damage to any stored electronic products at SMT. At the other extreme, all component handling areas are monitored and automatically conditioned to prevent low humidity ESD risk. The 60,000 sq.ft. of warehouse area is fully conditioned with 100 tons of rooftop HVAC units that were specially designed for moisture sensitive applications.
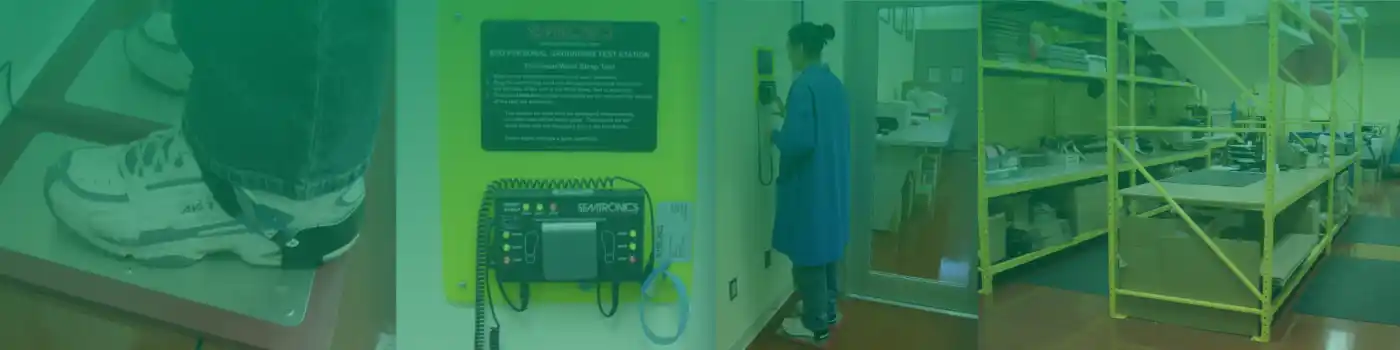
ESD Safety
Part of SMT’s commitment to protecting on-site material and delivering extreme product quality is the depth of our very proactive focus on ESD safety. Before any employee is allowed to enter the component inspection, testing, packaging or warehousing areas, they must first pass through a custom designed “ESD Airlock System”. This automated foot-wear and wrist-wear electronic test checkpoint must register a successful test to ground result in order to gain entry to these sensitive component handling areas.
All work surfaces are completely covered with high-quality ESD matting and constantly monitored with audible / visual alarms. ESD floors, mats, alarms, wrist & footwear are tested weekly to confirm the continuous integrity levels of all ESD safeguard systems in place at SMT Corp.
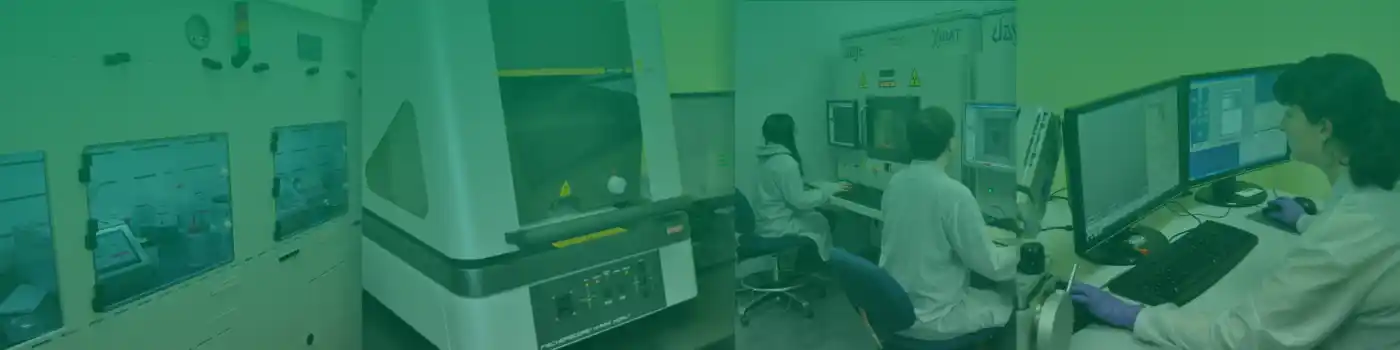
Labs
SMT Corporation has developed two state of the art, in-house authentication test labs certified to ISO17025. This rigorous certification includes acceptance for standard testing, nonstandard testing and lab-developed testing methods. All our test results are monitored for quality and integrity, our testing equipment is calibrated and well maintained and our written procedures are used for all aspects of lab activities. Our lab technicians include EE Engineers and certified inspectors. Our company is also certified to CCAP-101 for component authentication. In addition to our two state of the art labs, SMT has constructed 7,000 sq. ft of new lab space to incorporate our electrical functionality testing as well as our DNA applications.
We are now a fully serviced, one stop shop for the complete authentication and functionality of electronic components. Our lab equipment includes:
- 2 Keyence VHX-7000 Microscopes
- 24 Dinocam Digital Microscopes
- 12 Metallurgical Microscopes
- 2 Fischerscope XDAL X-Ray Fluorescence Systems
- 1 Innovox X-Ray Fluorescence System
- 2 DAGE X-Ray Inspection Systems
- DAGE Computerized Tomography (CT)
- 2 Glenbrook Jewel Box X-Ray units
- 2 Creative Electron, Automated Inspection R2R X-Ray Systems
- 2 Tescan Scanning Electron Microscopes
- 1 Oxford Instruments Energy Dispersive X-ray
- 1 EDX Energy Dispersive X-ray
- 2 GEN3 MUST Solderability Systems
- 4 Acid Etch Decapsulation Systems
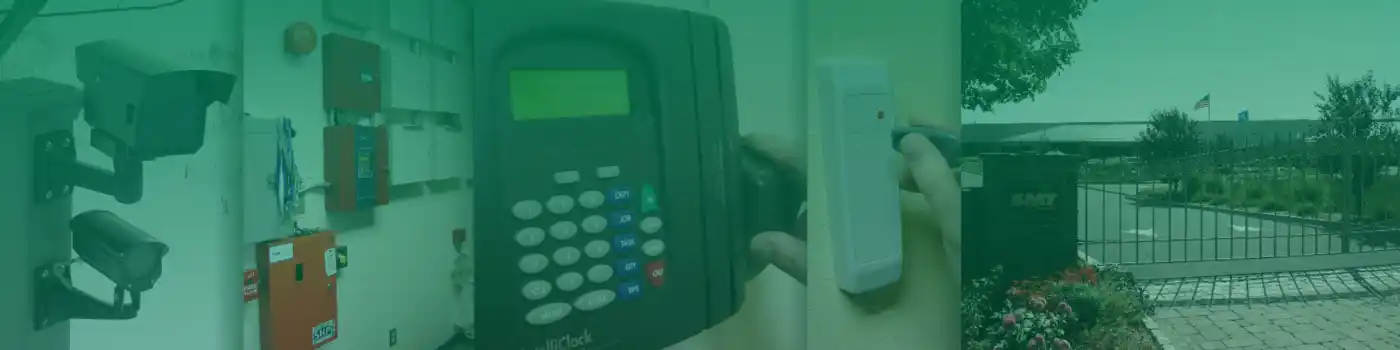
Security Systems
With the accountability of customer-owned consigned materials and the integrity of products and services provided to our customers, the SMT facility features the latest in security and fire systems monitored 24/7/365 by ADT. Additionally, our entire building and grounds are under constant IR video surveillance. All employees must be identified via a bio-scan in order to gain access into the SMT facility every single time. Once inside each employee’s movement is limited by unique FOB electronic access to the common and specific work areas they are assigned to.
The entire facility is sprinklered throughout with a redundant 120,000 gallon fire system reserve tank located under the building. The town fire department is located less than 1 mile from the SMT facility.
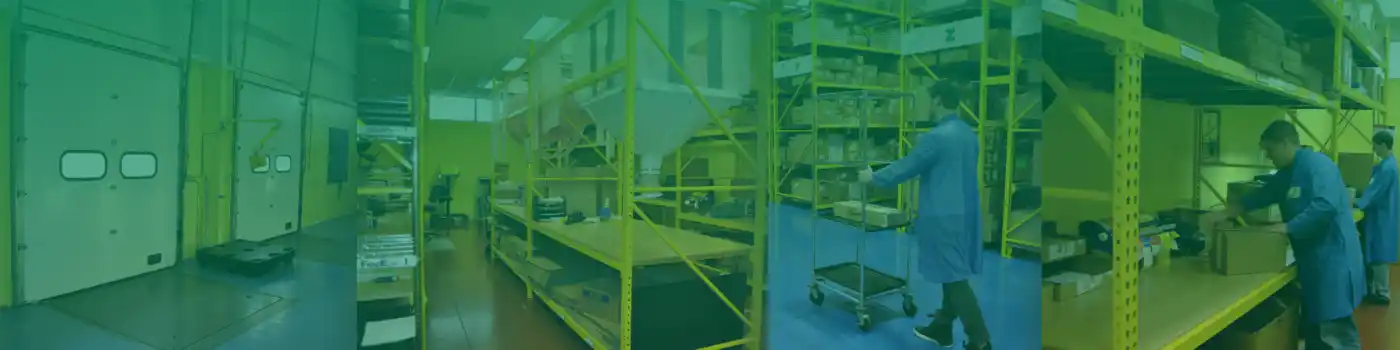
Shipping and Receiving
Our logistics department will ensure products are delivered in the fastest time possible. Our primary carriers are FedEx, UPS and DHL. All carriers make morning and evening scheduled pickups and deliveries to ensure fast and on-time daily shipments. ESD protocol is in effect in every area where components are handled. Shipping and receiving are not exceptions.
In addition, all components leaving the facility are properly packaged in anti-static material. Any components requiring air tight sealing are vacuum sealed with humidification cards. Receiving of components requires an initial inspection and preparation ensuring all parts are sorted and placed in protective anti-static bags. Upon receiving components, they go through the initial quality control procedures. After the components have passed inspection they are entered into our inventory database and placed into our warehouse.