Published: May 15th, 2023 | Updated: November 9th
Counterfeit Electronic Parts Threat Overview
Counterfeit electronic parts in the U.S. supply chain continues to grow in volume and sophistication, resulting in increased risk to defense and aerospace systems, as well as other critical infrastructure including communications, transportation, medical, energy, and the financial sector.
Risks due to counterfeit electronic parts include system failure, injury, and death – which may either be a result of substandard counterfeit components or intentional system sabotage when functions (e.g. trojans) are introduced into products and systems to cause harm or to exfiltrate critical information.
Particularly at risk are industries, including defense and aerospace, where long product lifecycles (20+ years) lead to diminished manufacturing sources and material shortages (DMSMS) and obsolescence issues because the electronics component average lifecycle is only 5-7 years (Blyler, Dangers of Counterfeit Semi Chips, 2020).
This report addresses several aspects of counterfeit electronic parts and provides recommendations to protect products and systems in critical U.S. applications.
Types of Counterfeit Electronic Parts
Currently, the most comprehensive counterfeit mitigation standard is SAE International AS6171; Test Methods Standard; General Requirements, Suspect/Counterfeit, Electrical, Electronic, and Electromechanical Parts:
AS6171 standardizes inspection and test procedures, workmanship criteria, and minimum training and certification requirements to detect Suspect / Counterfeit Electrical, Electronic, and Electromechanical (EEE) parts [referred to in this report generically as electronic parts]. The requirements apply once a decision is made, primarily out of necessity, to use parts that do not have traceability back to the original component manufacturer (OCM) or authorized distribution. The tests specified by this standard may also detect occurrences of malicious tampering, although the current version of this standard is not designed for this purpose. (SAE International, 2018)
Although recycling and misrepresenting genuine parts remain the most common forms of electronics counterfeiting – cloning and tampering are becoming more prevalent – and represents an increased risk to critical infrastructure.
Reverse engineering is one of the methods for cloning an authentic chip. In this technique, the counterfeiter physically removes the silicon die from the component package and will “delayer” the die. Once the chip has been completely delayered, the counterfeiter can then build a clone component using the reverse engineered, layer by layer silicon recipe (Blyler, Dangers of Counterfeit Semi Chips, 2020).
Another cloning technique is via functional emulation. Rather than reverse engineering the silicon die, a counterfeiter uses a similar silicon technology or die layout to achieve similar electrical functionality. The components are then packaged and marked to look like authentic devices. From an external perspective, the functional emulation clone device looks and functions like authentic devices.
Finally, cloning can be achieved by illicitly acquiring the original manufacturer’s IP (silicon mask files or recipes). This IP is a fabrication recipe that would allow a counterfeiter to illegally produce cloned components, provided they have access to adequate fabrication resources.
Clones and altered counterfeit chips are one of the key cyber-attack surfaces that Warren Savage, Chairman, CEO and President of IPextreme, identified in his keynote address at DesignCon 2020. “Such compromised chips are a serious problem for the semiconductor industry. For example, a counterfeit chip in a tank could feed sensitive information such as [location or armament] to an adversary. Rogue code in a fake semiconductor could shut down the air supply of an airliner. A counterfeit chip could be used to shut down a car in a ransomware attack.” (Blyler, Dangers of Counterfeit Semi Chips, 2020)
As an example of a possible cloned and tampered with counterfeit, SMT Corp., a recognized industry leader in counterfeit electronic parts mitigation, discovered a suspect counterfeit microcontroller (marked fraudulently as a ST Micro part number), in 2019, that was found in a point-of-sale (POS) device used for payment transactions.
SMT Corp. was able to extract and reverse compile code in the flash memory of this device and found references to the POS equipment maker which was based in China. The code could have been used to exfiltrate financial information from debit and credit cards.
There is particular concern about microcontroller counterfeits because of the potential for hardware trojans (hidden memory sectors or built-in sub-routines) that could allow third parties to extract data from systems. Microcontrollers are often interfaced to communications systems such as wired/wireless networks that can be remotely accessed.
According to Dr. Nicolas Williams, Director – Electronics Test & Analysis Labs at SMT Corp., widely recognized as the gold standard for counterfeit mitigation and electronics authentication and test, “the complexity of cloned devices being introduced into the defense supply chain has been steadily developing since the early 2010s. In 2012, SMT Corp. detected a cloned Inverter, a basic electronics logic device. In 2017, flash memory counterfeits were being discovered. In 2019, Microcontroller counterfeits became common. Today, we are seeing complex Field Programmable Gate Arrays (FPGAs) and modules. The complexity of electronics components being counterfeited is growing exponentially”.
The Market for Counterfeit Electronics
Due to their potentially high value, electronics are of particular interest to counterfeiters. As of 2022, the total global electronics market was estimated at $1.5 trillion, and is anticipated to reach $2.1 trillion in 2030, expanding at a CAGR of 5.5% (MarketWatch, 2023). The sustained growth of the electronics market, the increase in electronics complexity and density, the global “chip war”, geopolitical instability, and other factors provide increased incentive for would-be electronics counterfeiters. In a 2022 report, the Electronic Reseller Association International (ERAI) suggests that the number of counterfeit electronic products in circulation is increasing, and that businesses lose approximately $250 billion each year to counterfeit electronics products (Akhoundov, 2022).
The global electronic components market size supporting the electronics product market was valued at $186 billion in 2022. It is projected to reach $329 billion by 2031, growing at a CAGR of 6.5% during the forecast period (Straits Research, 2023). In 2019, the worldwide fake semi market was estimated at $75 billion according to Industry Week. (Blyler, Dangers of Counterfeit Semi Chips, 2020)
A 2021 study from the Boston Consulting Group and the Semiconductor Industry Association demonstrates how much chip production has moved away from its traditional strongholds – among them the United States – in recent years. As the figure shows, in 1990, Japan, Europe and the U.S. dominated semiconductor manufacturing; but with South Korea, Taiwan and mainland China entering the market, the three initial manufacturing locations were reduced to a combined market share of roughly 35% in 2020. The decline is projected to continue, if more slowly, through 2030. Even with some growth in the U.S. market driven by onshoring campaigns, most chip fabrication will continue to be from outside of the U.S. and Europe – with sources in Asia projected to dominate approximately 80% of the world’s semiconductor manufacturing (Buchholz, 2021).
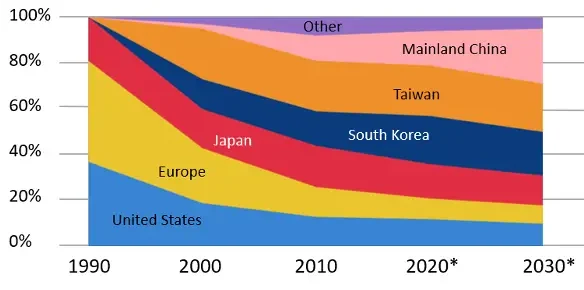
Change in Percentage of Global Semiconductor Manufacturing from 1990 to 2030* (*Projected)
Impacts on the U.S. DoD Electronics Supply Chain
Major defense systems are staying in service longer through extensive maintenance, upgrades, and modernization, and are significantly outliving original component production lifecycles. Counterfeit parts are increasingly entering the U.S. supply chain, primarily from China, and have been found across integrated circuits (ICs) and component parts including transistors, resistors, capacitors, fuses, etc.
Nick Martin, Director of the Defense Microelectronics Activity (DMEA) says that “Our DoD weapons systems are long in the tooth in terms of time in the field, and we need to make sure that there’s specific reliability requirements for the components that we put into them. Counterfeits or even cloned components will compromise the reliability” of this equipment (Gould, 2022).
Government-Industry Data Exchange Program (GIDEP) Program Manager Jim Stein notes that the Defense Department has seen counterfeits increase in number and sophistication over the last two decades, with batches of counterfeits increasingly hidden in authentic parts, making them harder to find (Gould, 2022).
Although standards are being proactively adopted by defense systems manufacturers such as Raytheon Technologies, Lockheed Martin, Northrop Grumman, L3Harris and General Dynamics, the implementation and enforcement of these standards across the aerospace/defense sector is slow and inconsistent. Adoption of the AS6171 standard is being driven by the potential implications of serious injury, loss of life, system failure and economic considerations. AS6171 represents the most accepted industry-wide standard for counterfeit EEE component mitigation.
Furthermore, the defense supply chain is extremely complex. For example, the F-35 relies on more than 1,700 suppliers at all levels providing roughly 300,000 parts. The Air Force’s network is even broader; the service said it depends on about 12,000 direct suppliers. But further down the supply chain, the network expands to about one million companies (Gould, 2022). Beyond the aerospace/defense sector there are few, if any, standards being adopted for counterfeit mitigation.
Current standards only address parts that are obsolete since in theory – if “active” parts (parts that are still for sale from the manufacturer) are available they are to be procured from an authorized channel. ERAI notes that 62.2% of counterfeit parts reported to them in 2022 were classified as “active” parts and only 32.5% were classified as “obsolete” and “NFND (not for new design)”. This data seems to question the notion that if you do not buy obsolete parts, you are less likely to encounter counterfeit parts (Akhoundov, 2022).
Real World Implications of Counterfeit Electronics
According to a 2012 Senate Armed Services Committee investigation, more than one million counterfeit electronic components were used in 1,800 instances affecting military aircraft and missiles (Senate Armed Services Committee, 2012).
The same investigation found that 84,000 suspect counterfeit electronic parts were inserted into the DoD supply chain by a single electronic parts supplier, Hong Dark Electronic Trade, of Shenzhen, China. Parts from Hong Dark made it into the Traffic Alert and Collision Avoidance Systems (TCAS) intended for the widely used C-5AMP airlifter, the C-12 Operational Support Aircraft, and the RQ-4 Global Hawk unmanned aircraft system. In addition, parts from Hong Dark made it into assemblies intended for the P-3 Anti-Submarine Warfare (ASW) aircraft, the Special Operations Force A/MH-6M helicopter, and other military equipment, including the Excalibur extended range artillery projectile, the Navy Integrated Submarine Imaging System, and the Army’s Stryker Mobile Gun (Senate Armed Services Committee, 2012).
In response to the recent death of an F-16 pilot, the Air Force Research Laboratory (AFRL) filed suit against multiple defense companies, alleging that “counterfeit parts” in a jet ejection seat system may have contributed to the death of the pilot in June 2020”. The suit contends that after 1st Lt David J. Schmitz’s death, AFRL determined his ejection system’s “malfunctioning” Digital Recovery Sequencer (DRS) contained “six suspected counterfeit Metal-Oxide Semiconductor Field-Effect Transistors (MOSFET), three suspected counterfeit serial flash memory chips, and a suspected counterfeit parallel flash memory chip.” (Gnau, 2022). The ejection seat is installed on aircraft across the Air Force including the F-15, F-16, F-22 and F-117 fighter jets, the A-10 attack plane, and B-1 and B-2 bombers, according to the manufacturer. (Cohen, 2022)
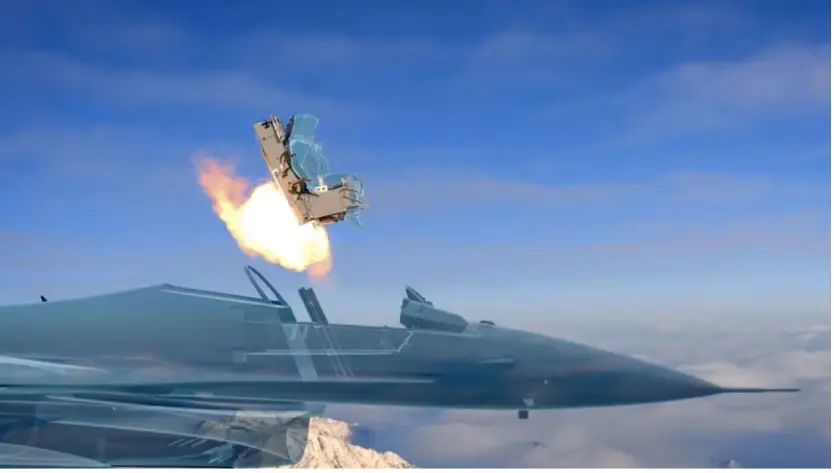
ACES II Ejection System (Collins Aerospace, 2020)
In 2018, Bloomberg Businessweek reported that the Chinese government inserted a stealth doorway into servers made by the Oregon-based company Elemental Technologies in the form of a tiny microchip. According to the report, the servers — with chips inserted at factories run by manufacturing subcontractors in China — could be found in Defense Department data centers, CIA drone operations and the onboard networks of U.S. Navy ships (Gould, 2022).
The Fukushima nuclear disaster of 2011 was partly attributed to the use of counterfeit electronics. The backup generators for the cooling systems of the nuclear reactors failed to function due to counterfeit electronics, which were not designed to withstand the conditions needed for the job. This led to multiple explosions, injuries, and radiation exposure, resulting in the deaths of two workers and the evacuation of tens of thousands of people.
Counterfeit Mitigation Techniques
Counterfeit parts are increasingly difficult to detect because of more complex counterfeit technologies and techniques, as well as the increasing complexity of global supply chains.
Published in late 2012, SAE AS6081, Fraudulent/Counterfeit Electronic Parts: Avoidance, Detection, Mitigation, and Disposition – Distributors, was adopted by some of the major component manufacturers and prime defense contractors as the required level of testing for material sourced from unauthorized distribution channels. Due to the increased sophistication of counterfeit electronics, SAE released AS6171 in 2016, subsequently revised in 2018, which defines a more robust, risk-based test methodology as compared to AS6081. In April 2023, AS6081 Revision A was released which eliminated specific test criteria from the standard, instead referencing the criteria of AS6171, solidifying AS6171 as the accepted industry standard for counterfeit EEE components identification. Even with the solidification of AS6171 as the accepted industry standard for counterfeit detection, SMT Corp reported that for 2022, with well over a thousand authentication test reports completed, 89.3% were at the older, antiquated AS6081 standard as opposed to the more robust AS6171 standard. The move to AS6171 testing is accelerating in 2023 but still only beginning to approach 50% of the total requirements.
As explained by Jason Romano, Chief Investigator and Subject Matter Expert at SMT Corp, “the minimum required counterfeit mitigation testing recommended by AS6171 is Moderate Risk Level 2, which requires both external and internal physical inspection of the component. Counterfeit components can have inconsistent markings, discoloration, resurfacing material, tooling marks, and numerous other subtle defects on the exterior package. To determine authenticity, a high-intensity digital microscope is used to examine each component for such defects, down to the sub-micron level. Clues of tampering require a trained eye and precise equipment to identify. The standards specify inspection tests that encompass basic visual inspection to more complex internal inspections. Additional tests and inspections can be performed to further increase the level of confidence.”
Some of the inspection tests required by AS6171 are depicted below (pictures courtesy of SMT Corp):
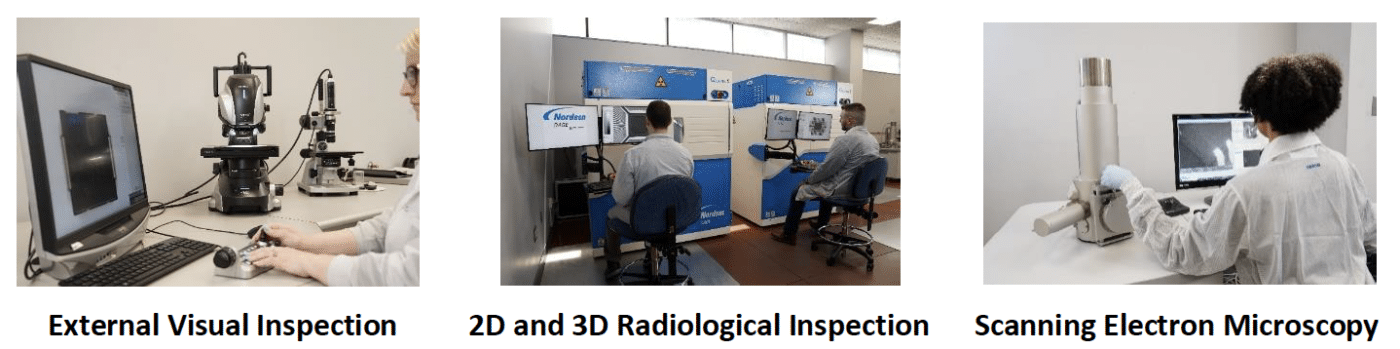
As a minimum, Moderate Risk Level 2 requires electrical testing of the static DC electrical parameters for active, complex devices or value measurements for passive components. This minimum level of required testing provides test coverage for the general component functionality. AS6171 includes optional recommended electrical testing such as measuring key electrical parameters, testing electrical components over operating temperature range, and burn-in. These additional tests are requirements for higher risk levels as determined by the Adjusted Risk Score per AS6171.
Current Policies
Section 889(a)(1)(B) of the Fiscal Year 2019 National Defense Authorization Act (NDAA) (Acqusition.Gov, 2019) prohibits recipients of federal contracting from using or procuring certain covered Chinese telecommunications equipment or services. GIDEP publishes data on companies that have been confirmed to pass through counterfeit parts yet there is no standard that enforces the avoidance of these companies.
The Fiscal Year 2023 NDAA also prohibits the federal government from entering or extending contracts with companies to procure electronic parts, products or services that include semiconductor parts or services from certain Chinese entities. The semiconductor prohibitions will not take effect until five years after the enactment of the Fiscal Year 2023 NDAA. Even with that, the volume of components (especially DMSMS parts) will make it difficult or impossible to eliminate China as part of the supply base. This means that testing of foreign sourced electronics is expected to increase.
For the DoD, DFARS (Defense Federal Acquisition Regulation Supplement) clauses addressing counterfeit electronic parts are included in procurement contracts. For example, DFARS 252.246-7007, which implements Section 818 of the 2012 NDAA, states that “the contractor shall establish and maintain an acceptable counterfeit electronic part detection and avoidance system.” The flowdowns establish that there should be a counterfeit avoidance program, not the inspection and test standards for such a program.
The U.S. Defense Logistics Agency (DLA) has defined more stringent standards (AS6171) but adoption across the defense industry is slow and inconsistent, primarily left up to defense industry prime contractors to proactively determine testing thresholds and applicability. Defense prime contractors are beginning to require compliance with standards; however, adoption is inconsistent and is expected to take years. Adoption beyond DoD programs to other U.S. critical infrastructure applications is uncommon and not yet required.
Research and Development Initiatives
Other methodologies being explored to determine if chips are authentic are via embedded hardware security primitives and sensors (does not apply to passive electronics). Hardware-based security primitives employ instance-specific and process-induced variations in electronic hardware as a source of cryptographic data. Hardware primitives include physical unclonable functions (PUFs) and true random number generators (TRNGs) to produce device-specific electronic fingerprints and random digital signatures. These fingerprints and signatures are used to generate cryptographic keys and IDs commonly used for device authentication, cloning prevention, etc. (Blyler, Staggering Chip Shortages Have Led to Counterfeit Tech. Can’t We Test for Fakes?, 2021)
One of the keynote presentations at DesignCon 2020 addressed DARPA’s Automatic Implementation of Secure Silicon (AISS) program. The goal of the program is to automate the process of adding various levels of security to today’s complex system-of-chip (SoC) designs. It would achieve this goal by allowing chip designers to explore the possible economics versus security trade-offs based on the expected application and intent of the chip. (Blyler, Threats to Chip Supply Chain Prompt Action, 2020)
The DARPA program builds on the previously discussed concepts of physical unclonable functions (PUFs), and true random number generators (TRNGs) to produce device-specific electronic fingerprints and random digital signatures. (Blyler, Threats to Chip Supply Chain Prompt Action, 2020)
Research into more sophisticated chip fingerprinting and validation is important to the future of counterfeit authentication, however there is still far to go to achieve a consensus across the semiconductor industry, the vast majority of which are outside of the U.S. Furthermore, even if such a consensus was reached, it would be years before it would affect most of the current obsolete and diminished material supply.
On June 12th, 2023, the Defense Microelectronics Activity (DMEA) released a Final Report on Machine Vision Pilot (MVP) and Microelectronic Authenticity and Security, Evaluation and Research (MASER). The report determined that machine vision technologies do not provide satisfactory solutions for counterfeit electronics mitigation and detection in a real-world environment. Further, the report concluded that careful source selection and the application of standards-based conventional testing, commensurate with the appropriate level of risk mitigation for the application, remains the industry best practice.
According to Dr. Williams at SMT Corp, “For electronics PUFs and TRNGs, and similar concepts such as DNA marking to be a viable counterfeit mitigation solution, it will require buy-in from the entire electronics components industry. Such a broad, industry wide agreement will only be feasible if mandated and enforced by multiple governments. Typically, agreements of this scope and scale will take a considerable amount of time to be drafted and agreed upon. Additionally, to be successful, manufacturers would have to be involved in DMSMS / obsolescence management, sharing, and confirming key information about unique ID markers (PUFs, TRNGs, etc.) so that third parties such as defense contractors, counterfeit mitigation testing labs, and component distributors would be able to use this shared information to detect counterfeit electronic components. Historically, original manufacturers have been reluctant to be involved in counterfeit mitigation efforts as from their perspective there is no financial incentive to support such efforts and there is only potential liability from their involvement.”
Conclusions and Recommendations
The threat of counterfeit electronic parts in the U.S. supply chain continues to grow in scope and scale. The issue of counterfeit electronic parts is simultaneously a financial loss, national security, and safety threat. As has been previously noted, electronics authentication standards exist, but are primarily applied to U.S. defense applications. Even then, adoption is slow and inconsistent and does not address other critical infrastructure applications. Emerging means of component authentication via encrypted code and DNA marking will take years to have a practical impact, if ever. In the near term, a comprehensive approach to counterfeit mitigation in the U.S. supply chain needs to consider sourcing, testing and risk avoidance.
Protecting U.S. infrastructure and avoiding the risk of counterfeit electronic parts in the supply chain necessitates adoption of the zero-trust policy being evaluated by DoD, which would assume no microelectronics are safe and all must be validated – as reported by Defense News in December 2022 (Gould, 2022). This entails allowing microelectronics into the supply chain only if testing demonstrates component authenticity, that there are no exploits built into them, and that they meet all requirements – including performance over environmental extremes. A zero-trust policy targeting components of unknown origin, and parts from areas where counterfeits are known to be active, is a minimum threshold.
A key aspect of risk mitigation is inspection and testing. U.S. Government partnership with industry – where testing and authentication occurs – to drive standards effectiveness for counterfeit detection and component authentication, is essential. While there are highly regarded “gold standard” counterfeit mitigation labs such as SMT Corp and Integra Technologies that go above and beyond current standards, there are also many labs that are suspected of cutting corners. While labs that have been accredited for AS6081 and AS6171 testing have processes that are audited and approved, there is no guarantee that the processes are followed rigorously. In fact, only a handful of test labs are currently accredited for AS6171 and two of those have had GIDEP alerts issued in 2023 for obvious escapes in the detection of suspect components. The U.S. Government must assess and designate “Trusted Labs” for counterfeit mitigation and electronics authentication. These labs must be periodically “pressure tested” by an independent authority such as the Defense Logistics Agency (DLA), Defense Microelectronics Activity (DMEA), or the Department of Justice (DoJ). For examples of the types of verification program needed, we can look to companies like SMT Corp that periodically introduce highly controlled counterfeit electronic parts into their workflow to ensure they are discovered by employees at the appropriate test and inspection steps.
In addition to establishing a “Trusted Labs” program, there should be funding for these labs. The execution of AS6081 and AS6171 inspections and tests are relatively straightforward when performed by experienced technicians, however these steps must be performed by competent technical resources that are trained to recognize the multitude of subtle differences between exemplar and suspect electronic components. According to Jason Romano at SMT Corp, “competent counterfeit identification technicians, or investigators, can take anywhere from 12 to 36 months to develop basic skills, whereas a higher level of knowledge can take years to develop. These investigators must become proficient in using a variety of tools and analytical processes, must gain an in-depth knowledge of electronics components, and must develop an in depth understanding of techniques being used to create counterfeit electronic components.” Funding would support these resources to maintain the highest level of training and skills development, enhance research and development into advanced detection methods, as well as support continuous improvement of tools and techniques for counterfeit identification.
Standards also must address sourcing – counterfeit avoidance – as an integral part of the counterfeit mitigation process. There are many electronics sourcing companies that outsource their testing to a third party, and test houses that do not source their own parts. This lack of ownership enables an ecosystem in which risks are compounded, resulting in a higher risk of counterfeit parts slipping through to critical systems. GIDEP publishes data on companies that have been confirmed to pass through counterfeit parts yet there is no standard that enforces the future avoidance, or rehabilitation, of these companies.
Another sourcing dynamic that results from the application of DoD regulations is the flow down of sole source policies. In most cases, gaining competitive bids is a good idea that promotes competition. However, in the case of hard-to-find diminished supply or obsolete parts, competition has the opposite effect of “heating up” the open market, thereby driving up prices. Of greater concern than the economic effects, competition for these obsolete parts can alert adversaries to the criticality of these parts.
These recommendations and standards need to be applied beyond U.S. defense applications to all critical infrastructure applications such as the mobile network grid, port security, air traffic control, financial transactions, implantable defibrillators, data centers, and the energy grid – not to mention emerging technologies such as quantum computing and artificial intelligence. Other U.S. government agencies including the Department of Energy, the Federal Aviation Administration, the Department of Homeland Security, the Food and Drug Administration, the Federal Communications Commission, and the National Transportation Safety Board must take note!
About SMT Corp
SMT Corp, located in Sandy Hook Connecticut, is an AS6081 / AS6171 accredited and industry recognized expert with full on-site sourcing, authentication, and electrical testing services to mitigate the risk of counterfeit, cloned, altered, or substandard products from entering the Aerospace and Defense industry critical supply chain.